3D-printers kunnen al een hoop, maar de plastics die we hiervoor gebruiken zijn nog lang niet zo sterk en duurzaam als we zouden willen. Wetenschappers doen daarom nog volop onderzoek naar nieuwe materialen.
Over een paar jaar hebben we allemaal een 3D-printer in huis! Deze voorspelling zingt al sinds de opkomst van de 3D-printers aan het begin van deze eeuw rond, maar toch wil het grote publiek er nog niet echt aan – op wat enthousiastelingen na. En dat terwijl deze nieuwe printers heel wat te bieden hebben. De theorie is namelijk heel simpel: je maakt een ontwerp, stopt dit met wat plastic in het apparaat en een paar uur later is het onderdeel voor je auto, keukenmachine of welk apparaat dan ook geprint.
Flink wat kennis
Het klinkt zo simpel, maar de praktijk blijkt toch wat weerbarstiger. “Met commerciële printers maak je prima een fluitje of kleine gadget”, vertelt Vincent Voet, associate lector bij het lectoraat Duurzame Kunststoffen van NHL Stenden. “Maar producten printen die je echt intensief wil gebruiken vergt toch wel flink wat kennis, zowel van het ontwerpen, het materiaal en de printer zelf.”
De meeste 3D-printers vind je daarom bij bedrijven, universiteiten en hogescholen. Bij de kennisinstellingen gebruiken ze printers niet zo zeer om spullen te printen, maar vooral voor onderzoek. Het is een relatief snelle manier om een onderdeel of zelfs heel product te maken. Ze gaan bijvoorbeeld na of je botimplantaten kan printen, bouwen er auto’s mee of ontwerpen met deze techniek kleding.
Hoewel deze printers inmiddels al enkele tientallen jaren bestaan, is er nog een hoop te verbeteren. Bijvoorbeeld de materialen die in de printer gaan en waarmee je dus van alles bouwt. Die willen onderzoekers nog steviger maken, beter hittebestendig of duurzamer. “De kunststoffen die we momenteel gebruiken voor 3D-printen zijn allemaal polymeren, lange molecuulketens die samen een stevig materiaal vormen”, zegt hoogleraar supramoleculaire polymeerchemie Rint Sijbesma van de TU Eindhoven. “Maar we gebruiken slechts een heel klein percentage van alle bekende polymeren voor 3D-printers. Er is dus nog een hoop te ontdekken.”
Verschillende printers
Welke materialen onderzoekers nu gebruiken, hangt af van het soort 3D-printer. “Voor de meest bekende vorm van 3D-printen, FDM, gebruik je lange plastic draden, of filamenten”, legt Voet uit. Deze draden zijn meestal gemaakt van polymelkzuur (PLA) of acrylonitril-butadieen-styreen (ABS). Voet: “In de printer smelten deze plastics en vervolgens worden ze laag voor laag gespoten in de ingestelde vorm.” Zo bouw je dus een nieuw product naar wens.
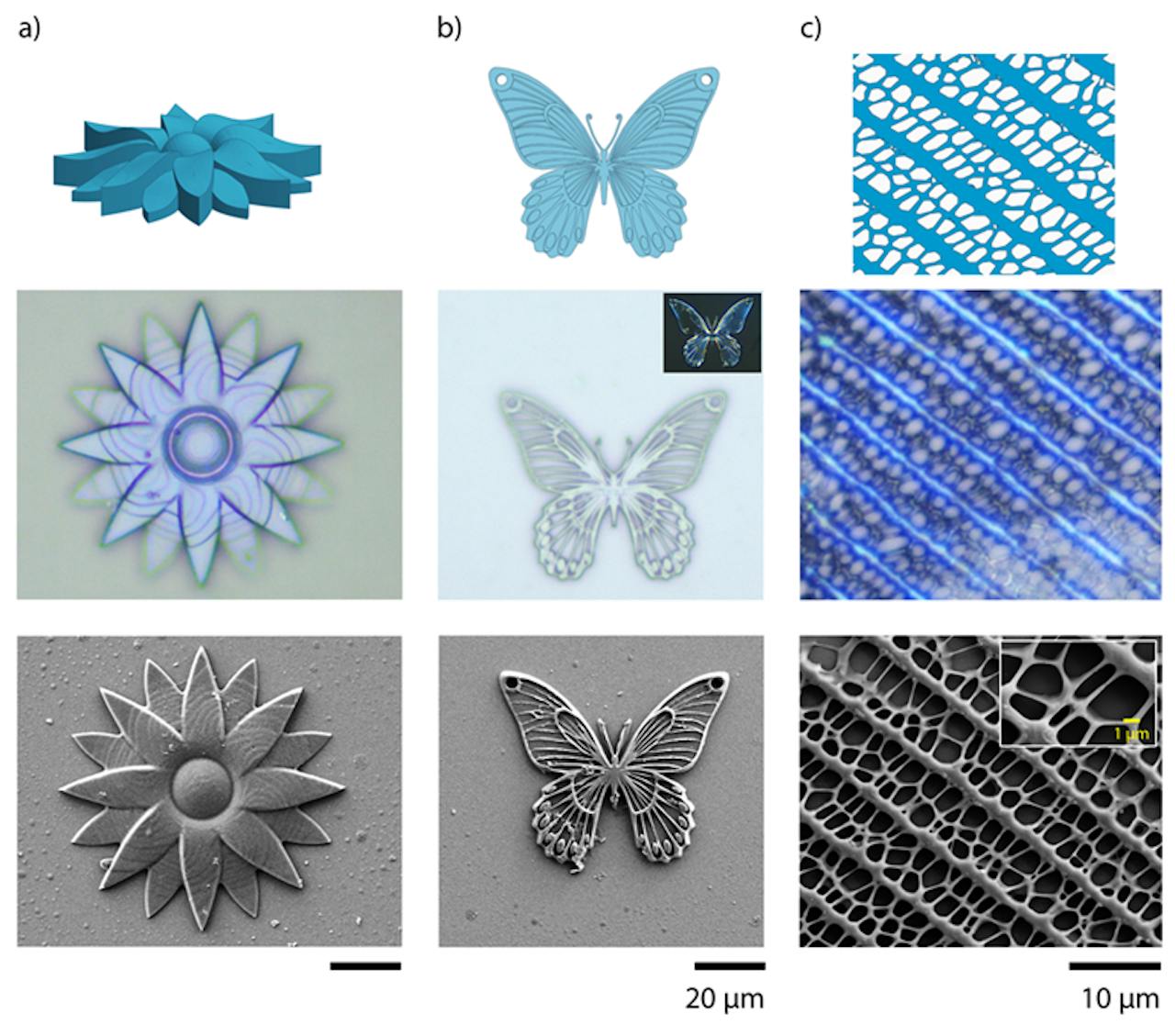
In de laboratoria van de TU Eindhoven worden verschillende 3D-print technieken onderzocht. Deze vormen zijn gemaakt met fotopolymerisatie printers.
Via Albert Schenning, met toestemmingEen andere manier van printen is met zogenoemde fotopolymerisatie printers, ook wel harsprinters genoemd. Hier stop je een vloeibare inkt in. “Vervolgens gebruikt de printer een UV-lichtbron om te zorgen dat deze moleculen op de juiste plek een hard materiaal vormen”, zegt Voet. “Hiervoor gebruiken we vaak acrylaatharsen, een beetje dezelfde materialen die de tandarts gebruikt om gaatjes te vullen.”
Tot slot kun je ook 3D-printen met een proces genaamd sintering. Deze printers gebruiken een poeder, meestal Nylon-12. “Met behulp van een laser laat je heel specifiek poederdeeltjes aan elkaar smelten”, zegt Sijbesma.
Voor- en nadelen
Elk van deze 3D-printers heeft zijn eigen voordelen en problemen. Zo maak je bij harsprinters en sintering zogenoemde thermoharders: stevige plastics die meestal lang meegaan, maar die je ook vrijwel niet kunt recyclen. “De enige manier om een thermoharder opnieuw te gebruiken is door hem simpelweg in stukken te hakken”, vertelt Sijbesma.
De plastics die uit de FDM komen zijn daarentegen thermoplasten: plastics die je weer om kunt smelten. Sijbesma: “Deze zijn in principe te hergebruiken, maar het nadeel is dat de producten die je hiermee print vaak zogeheten kruip vertonen. Ze veranderen langzaam van vorm omdat de bindingen tussen de verschillende lagen niet stevig genoeg zijn.”
Plastic hergebruiken
Om deze problemen op te lossen werkt Sijbesma aan een nieuwe klasse van polymeren: vitrimeren. “Dit zijn normale polymeren, maar ze hebben een belangrijke eigenschap”, zegt Sijbesma. “Ze vormen namelijk een dynamisch netwerk van zogenoemde esterverbindingen. Dat wil zeggen dat de esterverbindingen ook weer los kunnen laten zonder dat het polymeer kapot gaat.”
Dit materiaal combineert volgens Sijbesma het beste van twee werelden: “Het netwerk dat ze vormen lijkt op dat van een thermoharder, maar omdat we dit netwerk ook weer kunnen verbreken, is het waarschijnlijk mogelijk om het plastic na gebruik gewoon te smelten en te hergebruiken.” Dit biedt mogelijkheden voor nieuwe toepassingen. “We werken samen met een bedrijf dat met 3D-printers op maat gemaakte kaakprotheses wil printen. Dat is met de huidige materialen ook al wel mogelijk, maar vitrimeren zorgen ervoor dat deze protheses duurzamer worden, omdat je het materiaal weer kunt hergebruiken als de persoon de prothese niet meer nodig heeft.”
Poeder of draad
Maar dan moeten de onderzoekers natuurlijk nog wel hun materiaal testen. De vitrimeren die ze tot nu toe maakten waren echter nog niet goed genoeg voor de huidige 3D-printers. “We willen graag een poeder maken voor sintering, of een draad voor een FDM-printer. Maar de bindingen in deze vitrimeren zijn nog te sterk en laten niet snel genoeg los, dus kunnen we ze niet goed verwerken”, aldus Sijbesma.
Om dit wel voor elkaar te krijgen, heeft hij een katalysator toegevoegd. “We hebben aan het polymeer een zogeheten sulfonzuurgroep, dat is een zwavelmolecuul met drie zuurstofmoleculen, toegevoegd die de esterverbindingen kan verbreken.” De eerste testen met dit nieuwe vitrimeer zijn inmiddels gedaan. “Het materiaal is nu veel beter te bewerken. We willen eind deze maand ons eerste filament maken.”
Hergebruiken
Sijbesma denkt dat dit materiaal de deur opent voor nog meer nieuwe en betere materialen. “Eigenlijk is het toevoegen van die zuurgroepen een trucje, dat je misschien wel op veel meer polymeren kunt toepassen. Er zijn meer polymeren die dezelfde soorten verbindingen hebben, en als je zo’n katalysator toevoegt kun je deze materialen misschien ook wel dynamisch maken, en zorgen dat we steeds meer mogelijkheden hebben om deze plastics te recyclen.”
Ook Voet werkt aan recycling. “Op dit moment ontwikkelen we thermoharders uit 3D-printers, die we recyclebaar maken. Daarnaast maken we nieuwe, duurzame grondstoffen uit bijvoorbeeld biomassa.” Met zijn collega’s ontwikkelde hij onder andere al printerdraden versterkt met natuurvezels. “We hebben hout- en katoenvezels toegevoegd”, zegt Voet. “Dit bleek een goede, natuurlijke manier om het plastic sterker te maken. De plastics met houtvezels zijn zelfs al commercieel verkrijgbaar, en kunnen gebruikt worden in de bouw.”
Sojabonen en cashewnoten
Op het moment focust de associate lector zich op nieuwe harsen. “We gebruiken al sojaboonolie of olie uit de schillen van cashewnoten om de fossiele harsen te vervangen”, vertelt Voet. “Deze soorten olie bevatten al de juiste bouwstenen, alleen moeten de moleculen nog worden bewerkt. Dat blijkt echter niet veel moeite, slechts een paar reacties en je inkt is klaar.”
Met dit soort nieuwe grondstoffen maken we 3D-printers volgens Voet gemakkelijk duurzamer. “Deze nieuwe inkt werkt op dezelfde manier als de traditionele hars. Je hoeft niet eens de instellingen van je printer aan te passen. Het enige obstakel is in feite nog de beschikbaarheid.” Maar ook dat moet op termijn op te lossen zijn, denkt hij. “Veel soorten plantenolie zijn geschikt als inkt; in Amerika gebruiken ze bijvoorbeeld gebruikt frituurvet. Dat willen wij ook onderzoeken met lokale reststromen.”
Hoe veel duurzamer deze nieuwe inkten precies zijn, is volgens Voet lastig te zeggen. “Wat betreft de grondstoffen is het duidelijk: onze inkt is voor meer dan negentig procent gemaakt van hernieuwbare grondstoffen, terwijl huidige inkten volledig fossiele grondstoffen gebruiken. En je kunt ze recyclen, dus dat scheelt ook. Maar ze zullen wellicht ook wat duurder zijn.” Kortom, de exacte cijfers hebben ze nog niet. “Die komen pas als we deze inkten echt op commerciële schaal kunnen vergelijken.”
Uiteindelijk hoopt Voet de kringlopen beter te sluiten. Volgens Sijbesma zullen dit soort ontwikkelingen nog wel even doorgaan. “Elke toepassing van 3D-printen zal weer net een ander materiaal nodig hebben.”