Chemische fabrieken zijn indrukwekkend om te zien, maar je wandelt er niet zomaar even binnen. Tenzij het de ‘Dag van de Chemie’ is, zoals onlangs op 26 september. Kennislink ging kijken bij zinkproducent Nyrstar in Budel.
Geen gepruts met microgrammen in een reageerbuisje. Of ingewikkelde structuurformules van moleculen met nog ingewikkelder namen. Bij Nyrstar in het Brabantse Budel doen ze niet moeilijker dan nodig is: ze maken zink. Nou ja, eigenlijk maken ze veel meer dan alleen zink.
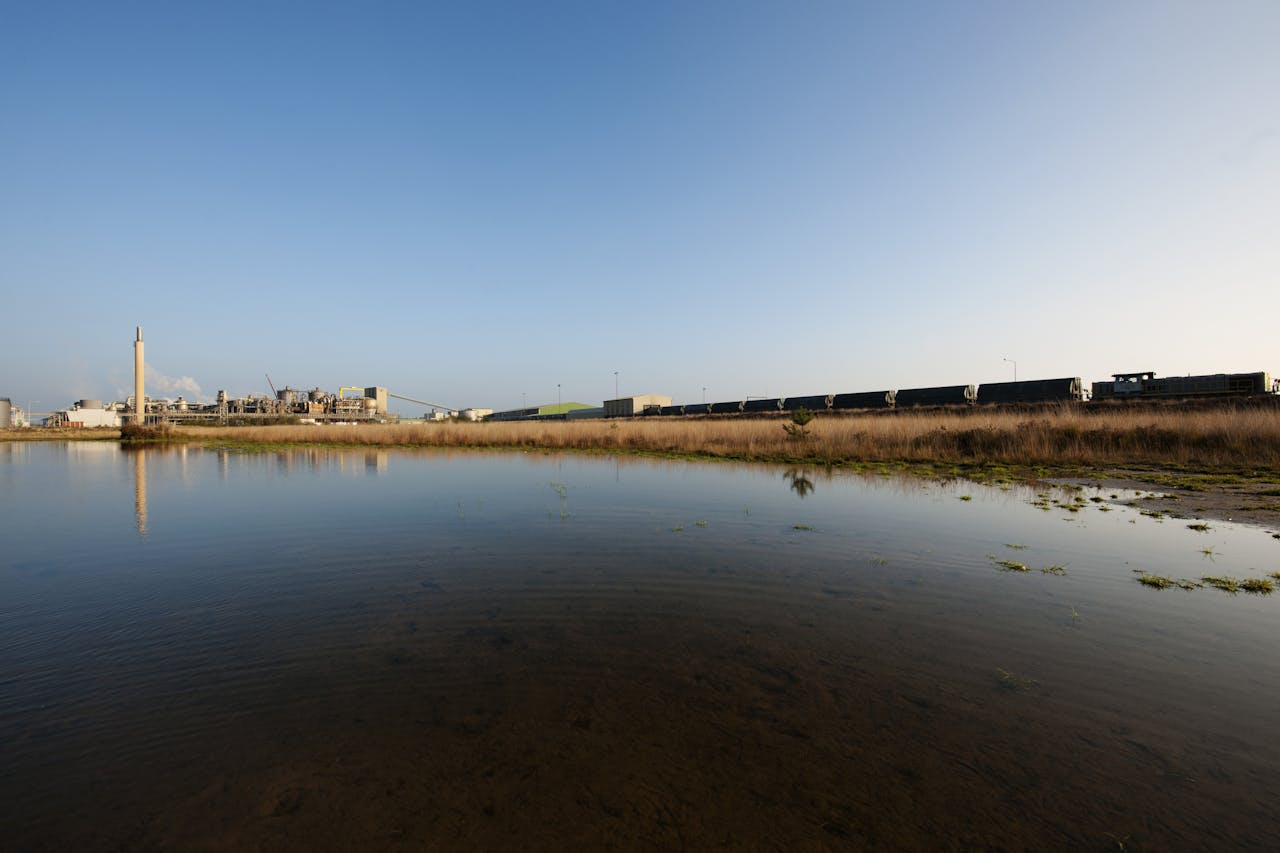
Dit is chemie zonder witte jas, maar met een veiligheidshelm, stevige schoenen en soms ook gehoorbescherming. Bij Nyrstar, onderdeel van een internationaal mijnbouw- en metalenwinningsconcern, denken ze niet op de schaal van het laboratorium. Nee, hier draait alles om kilotonnen (=1000×1000 dus 1 miljoen kilogram). Echte old school chemie met grote reactoren, stampend lawaai en een wirwar aan enorme buizen en pijpen. De rondleiding tijdens de Dag van de Chemie is een wandeling van 3,5 kilometer en dan heb je nog lang niet het hele terrein gezien.
Maar hoe klassiek deze chemische plant ook oogt, wat hier gebeurt is zeer modern. Reststromen worden omgezet in bruikbare producten of hergebruikt, waardoor er bijna geen afval ontstaat. Afvalwarmte wordt zoveel mogelijk benut in de fabrieken. En dankzij de twee biologische afvalwaterzuiveringsinstallaties op het terrein vormt deze fabriek de belangrijkste waterbron voor de nabijgelegen Tungelroyse Beek.
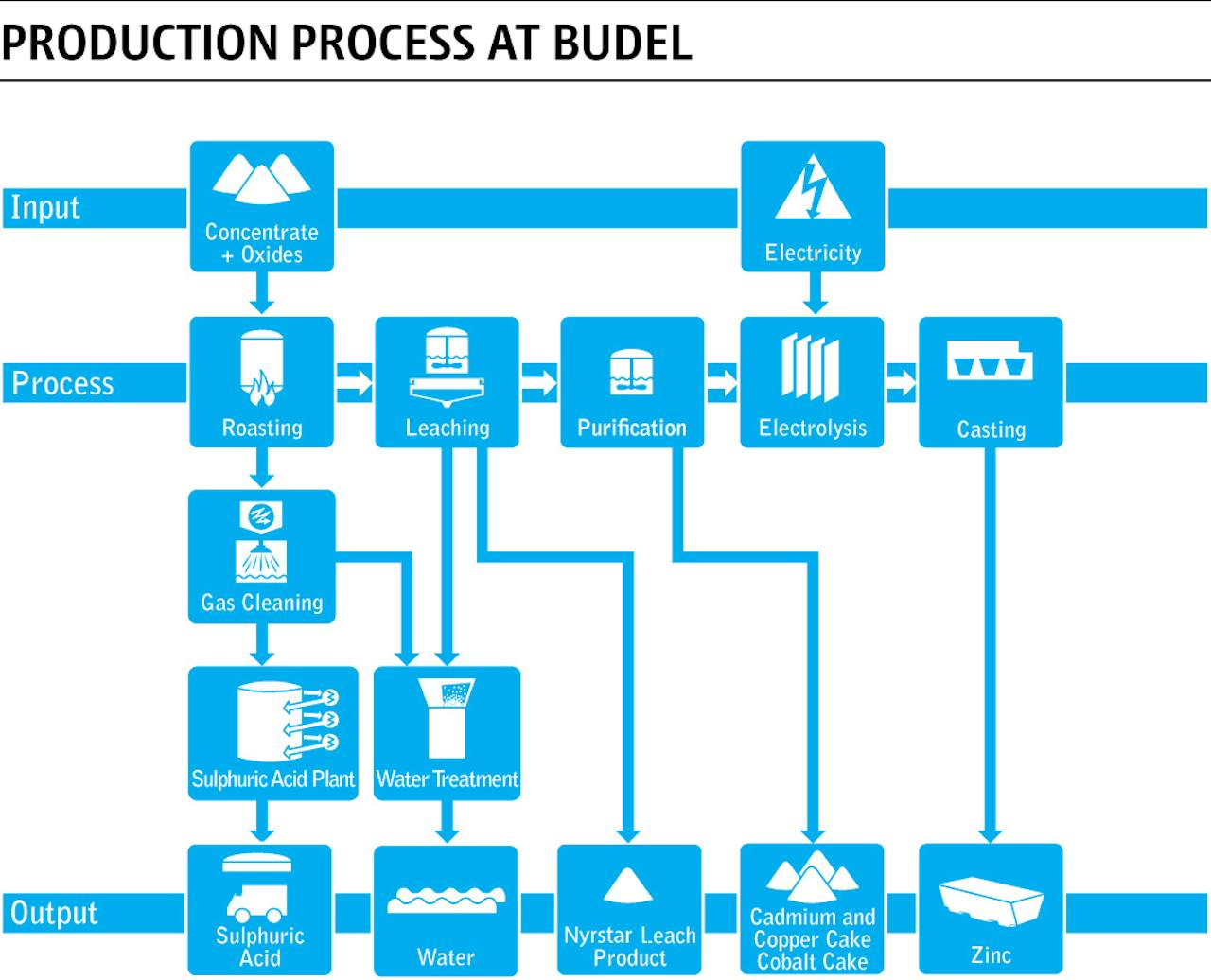
Roost(er)en
We wandelen over de plant in de volgorde van het proces; van het ruwe materiaal tot de blokken zink voor de klanten. Nyrstar maakt zink, maar wat valt er eigenlijk te ‘maken’ aan een metaal dat je uit de grond haalt? Zuiveren zou een betere term zijn, want het hele productieproces is erop gericht om het zink in een zo zuiver mogelijke vorm te verkrijgen. Het begint allemaal bij het zinkconcentraat, het ruwe materiaal dat de grondstof vormt. “Ongeveer dertig procent van ons uitgangsmateriaal is gerecycled zink. De rest is vers gedolven in verschillende mijnen”, vertelt rondleider Cris Copini, productiemanager bij Nyrstar Budel. Via het spoor komen dagelijks vanuit de haven in Antwerpen 25 wagons met elk ongeveer 67 ton (67.000 kilo) zinkconcentraat aan in Budel.
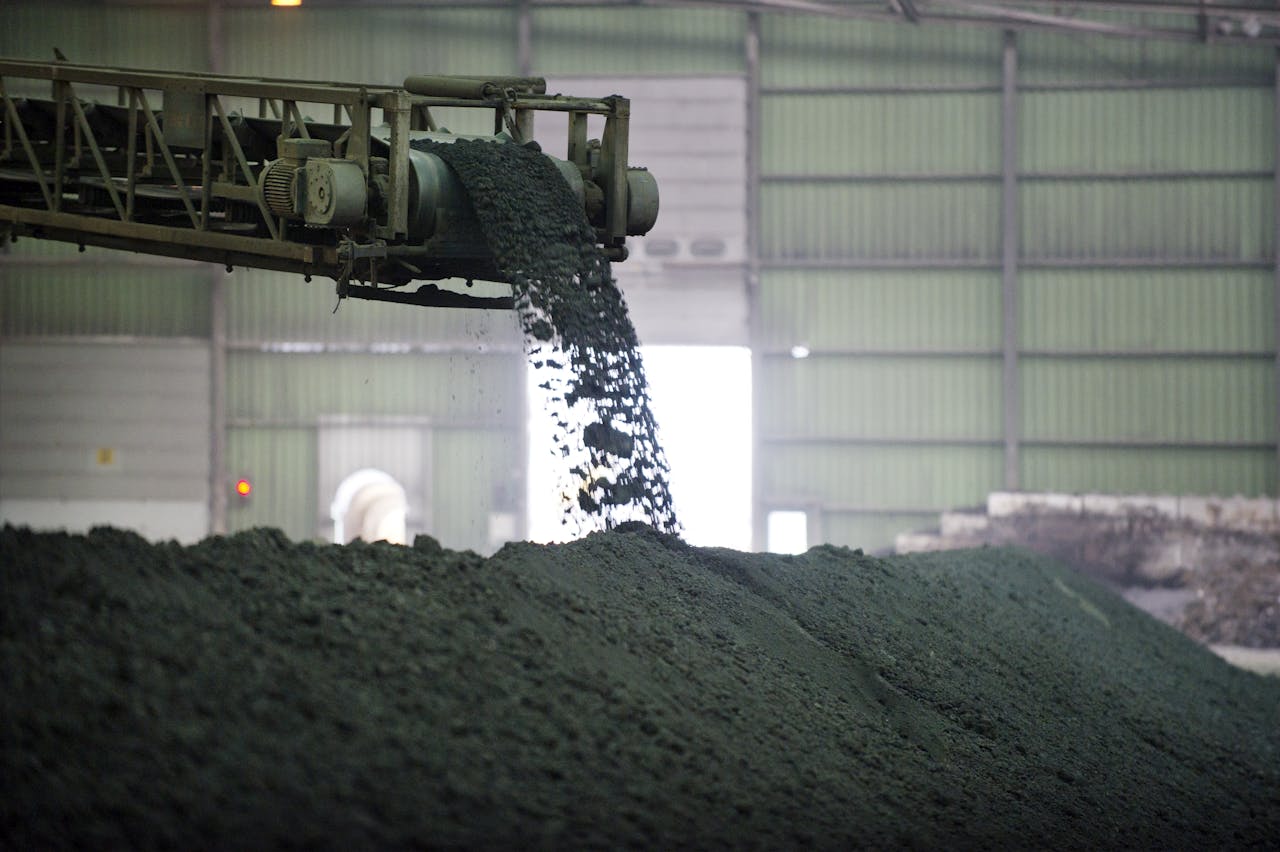
Als eerste werpen we een blik in de ertshal, waar het ruwe materiaal wordt gemengd om een zo constant mogelijke samenstelling te leveren. Het oogt als een vrij egale massa kleine, donkere korrels. “Gelukkig wel”, aldus Copini. “Hoe egaler de uitgangsstof, hoe efficiënter de volgende stap in het proces verloopt.” Gerekend naar droge massa bevat dit ruwe materiaal ongeveer 55 procent zink en 30 procent zwavel. Veel van het zink zit gebonden aan het zwavel als zinksulfide, maar dat is geen goed startmateriaal. De zwavel moet eruit en dat gebeurt in de eerste processtap: roasting.
We zijn ondertussen aangekomen bij de _roasting_-fabriek en Copini wijst de verschillende onderdelen aan. Een groot rond vat met daaronder een soort trechter en aan de bovenkant verschillende buizen; dat is kort gezegd de hele opstelling. “Het zinkconcentraat wordt via een gesloten transportband vanuit de ertshal naar dit grote vat getransporteerd. Van onderen blazen we dan lucht door het materiaal.” Door de reactie met zuurstof uit de luchtstroom gaat het zinksulfide over in zinkoxide (ZnO), een vaste stof, en zwaveldioxide (SO2), een gas. Bij deze reactie komt veel warmte vrij, waardoor de temperatuur oploopt tot zo’n 950 graden.
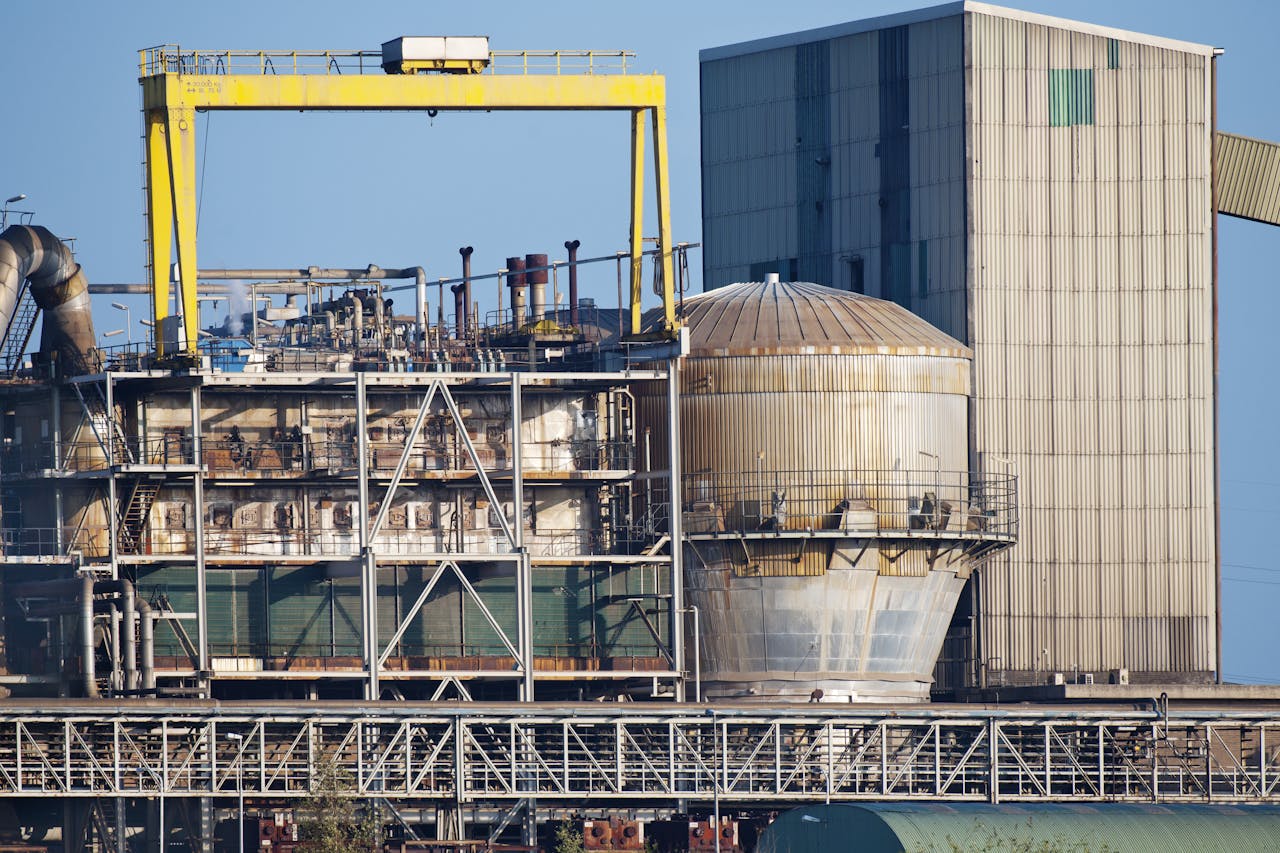
Zwavelzuur
Het zinkoxide, dat ze hier ‘roostgoed’ noemen, kan nu door naar de volgende stap: de loging. Maar voordat we daar gaan kijken horen we eerst wat er met het zwaveldioxide gebeurt. Dit is een sterk vervuilend gas dat niet zomaar de buitenlucht in mag. Gelukkig is er een nuttige bestemming, want zwaveldioxide is een prima grondstof voor zwavelzuur (H2SO4), een van de meest gebruikte industriële chemicaliën. “Het hete gas wordt in meerdere stappen afgekoeld en gezuiverd, waarbij vrijgekomen warmte wordt opvangen en als stoom hergebruikt in de loging. Het afgekoelde zwaveldioxide gaat als grondstof naar onze zwavelzuurfabriek”, vertelt Copini. Hij wijst op een oranje, bovengrondse pijpleiding. “Hierdoor gaat het zwavelzuur naar de binnenhaven, waar het in schepen wordt gepompt. Naast zink is zwavelzuur ons belangrijkste product. We maken jaarlijks zo’n 360 kiloton.”

Ondanks het hergebruik van de warmte zien we dikke witte pluimen opstijgen. Per uur vliegt er zestig m3 waterdamp de lucht in. Dat is zonde, vindt Copini. “Maar we hebben nog geen manier gevonden om deze warmte nuttig in te zetten. Je zou het wellicht kunnen gebruiken voor stadsverwarming. Maar ja, hier in het landelijke gebied heb je daar weinig aan.” De uitstoot is een verspilling, maar het is niet schadelijk, benadrukt Copini. “De roasting en de zwavelzuurfabriek hebben sinds 2000 een extra zuiveringsstap om NOx weg te vangen.” NOx is een verzamelterm voor verschillende (schadelijke) stikstofoxiden.
Metaalkoeken
De volgende stop is de loging. Het zinkoxide, dat ze hier ‘roostgoed’ noemen, bevat 60 tot 65 procent zink en daarnaast een uitgebreide collectie aan andere metalen. Koper, cadmium, lood, zilver, nikkel, ijzer, kobalt en germanium – om maar wat te noemen. Deze worden allemaal na winning opnieuw gebruikt.
Het roostgoed wordt voor zover mogelijk opgelost in zwavelzuur. Het ijzer in de oplossing slaat dan neer, wat wil zeggen dat het een vaste stof gaat vormen. Samen met onoplosbare componenten zoals loodsulfaat vormt het Budel Leach Product (BLP). “BLP bevat relatief veel lood en is daarom een goede grondstof voor loodsmelters”, vertelt Copini.
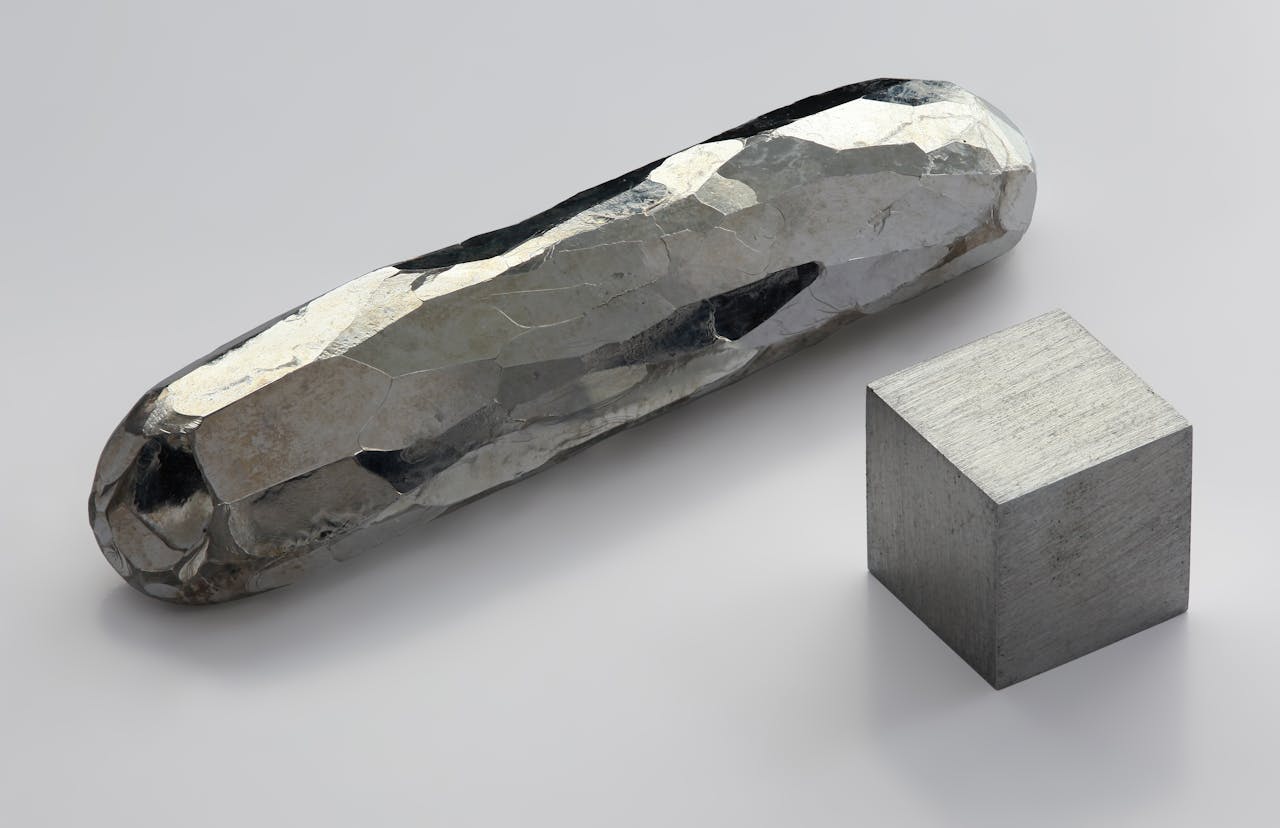
Om de overige metalen te verwijderen, moet er een tandje bij. Als eerste volgt de koude zuivering. Koud betekent hier overigens 72 graden. Bij deze temperatuur en na toevoeging van wat zinkstof lukt het om ook het koper en cadmium uit de oplossing te halen. Koper wordt als een ‘koek’ gewonnen die 75-85 procent koper bevat. Het cadmium wordt als enige als een zuiver metaal gewonnen en vindt zijn weg naar onder meer de batterijenindustrie. Om tot slot ook het laatste metaal, kobalt, te verwijderen is een warme zuivering nodig. De temperatuur gaat naar 87 graden en er wordt nog wat extra fijn zinkstof, antimoon (ook een metaal) en kopersulfaat toegevoegd. Pas dan lukt het om het kobalt een koek te laten vormen. Deze bevat ongeveer vijf tot zes procent kobalt en dit is een goed uitgangsmateriaal voor verschillende toepassingen. Kobalt wordt bijvoorbeeld gebruikt om staal specifieke eigenschappen te geven, zodat het niet vervormt bij hoge temperatuur of slijt bij intensief gebruik.
Dan is er nog een zuiveringsstap te gaan. Niet om een metaal te verwijderen, maar om calcium eruit te halen. “Dat doen we na koeling van de oplossing in het champagneglas”, legt Copini uit. “Zo noemen we het enorme trechtervormige vat waarin we het calcium laten neerslaan tot gips. Eenmaal ontgipst is het eindresultaat een zuivere zinkoplossing die 150 gram zink per liter bevat.” Tijd om eindelijk het zink in handen in te krijgen.
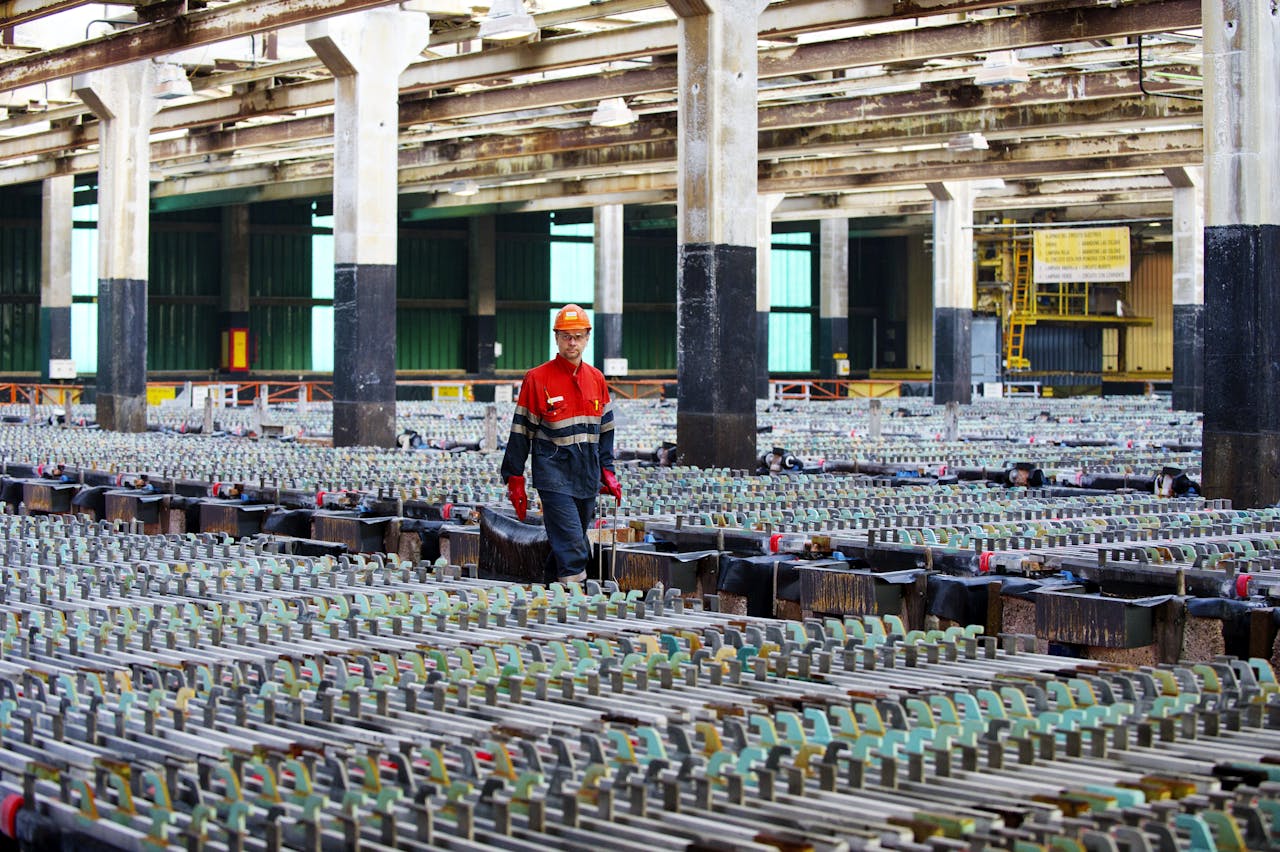
Zinkafzetting
Daarvoor moeten we naar de elektrolysehal. Dit is een indrukwekkend gezicht. Een enorme hal, waar een licht zure lucht hangt, met daarin eindeloos veel rijen bakken waar grote aluminiumplaten in hangen. Copini: “Dit zijn allemaal elektrolysecellen waar we stroom doorheen laten lopen. De grote platen in de bakken zijn de kathodes, de negatief geladen polen. De cellen vullen we met de zuivere zinkoplossing. Zinkatomen zijn positief geladen en door stroom te laten lopen door ieder circuit wordt het zink naar de kathodes getrokken en zetten zich daar af.” Na ongeveer 32 uur is de zinklaag op de kathodes drie millimeter dik. Dat is het moment om de platen uit de cellen te halen. De dofgrijze zinklaag wordt er als een plaat vanaf ‘gestript’. De zinkplaten van vijftig kilo per stuk zijn nu klaar voor hun eindstation: de gieterij.
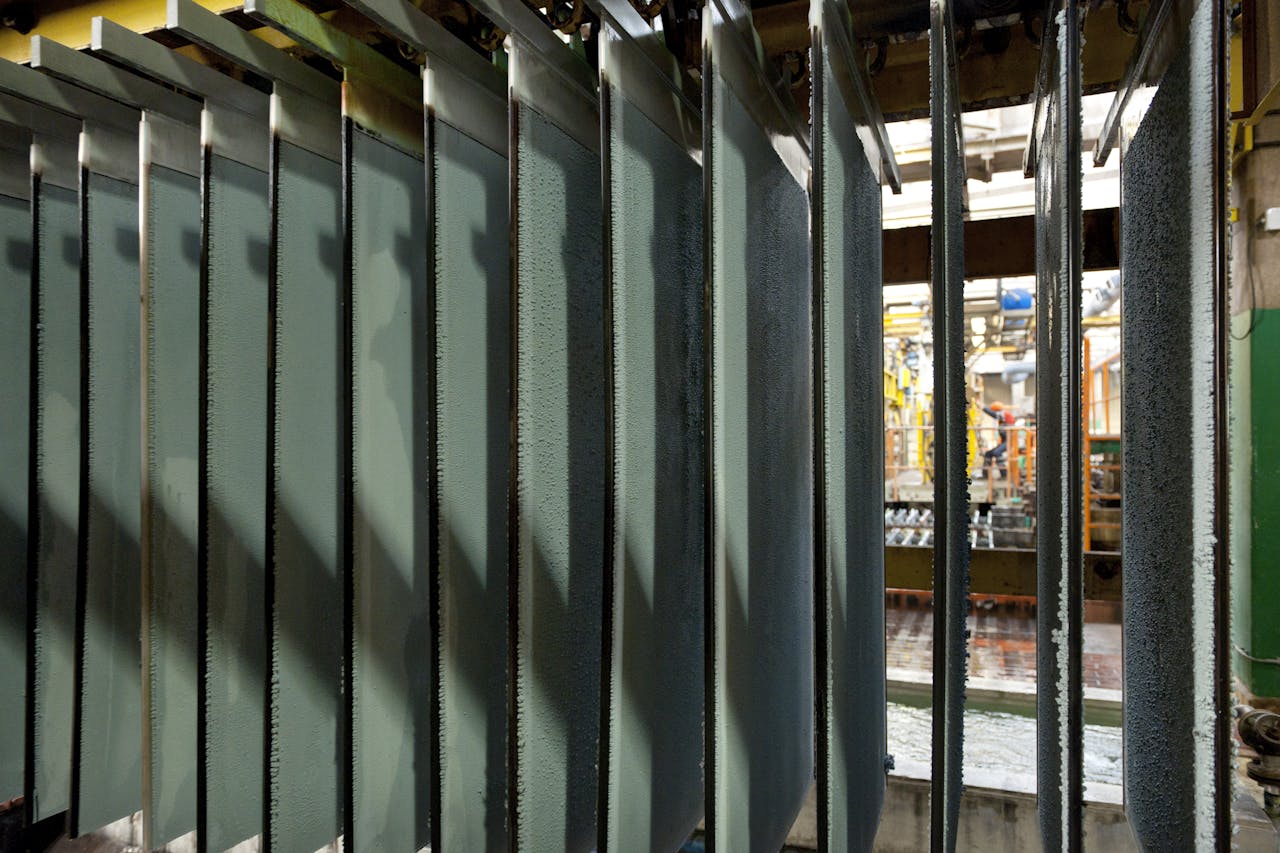
Het is dat er in de gieterij geen man met een hamer op een aambeeld staat te slaan, anders zou je denken dat je een smederij bent binnengewandeld. Op een luid ratelende loopband komen grote bakken voorbij waarin gloeiend heet (550 graden) en onwaarschijnlijk mooi glanzend zink stroomt. Eenmaal in de bakken schieten vanuit branders steeds vlammen op, om te voorkomen dat het zink te snel afkoelt. Dat zou leiden tot scheuren in de zinkblokken. “Per dag gieten we hier achthonderd ton vrijwel zuiver zink in blokken van verschillende omvang”, vertelt Copini. De kleinste zijn 25 kilo, de grootste 4000. Het belangrijkste product is het _Special High Grade_-zink dat meer dan 99,995% zuiver is. Maar niet iedere toepassing vraagt om zuiver zink en daarom maakt Nyrstar ook enkele legeringen; combinaties van metalen. “Dat is afhankelijk van wat de klant vraagt. De toevoegingen veranderen de eigenschappen van het zink. Aluminium maakt het buigzaam. Voeg je koper toe, dan krijg je messing dat wordt gebruikt in kranen en fittingen.”
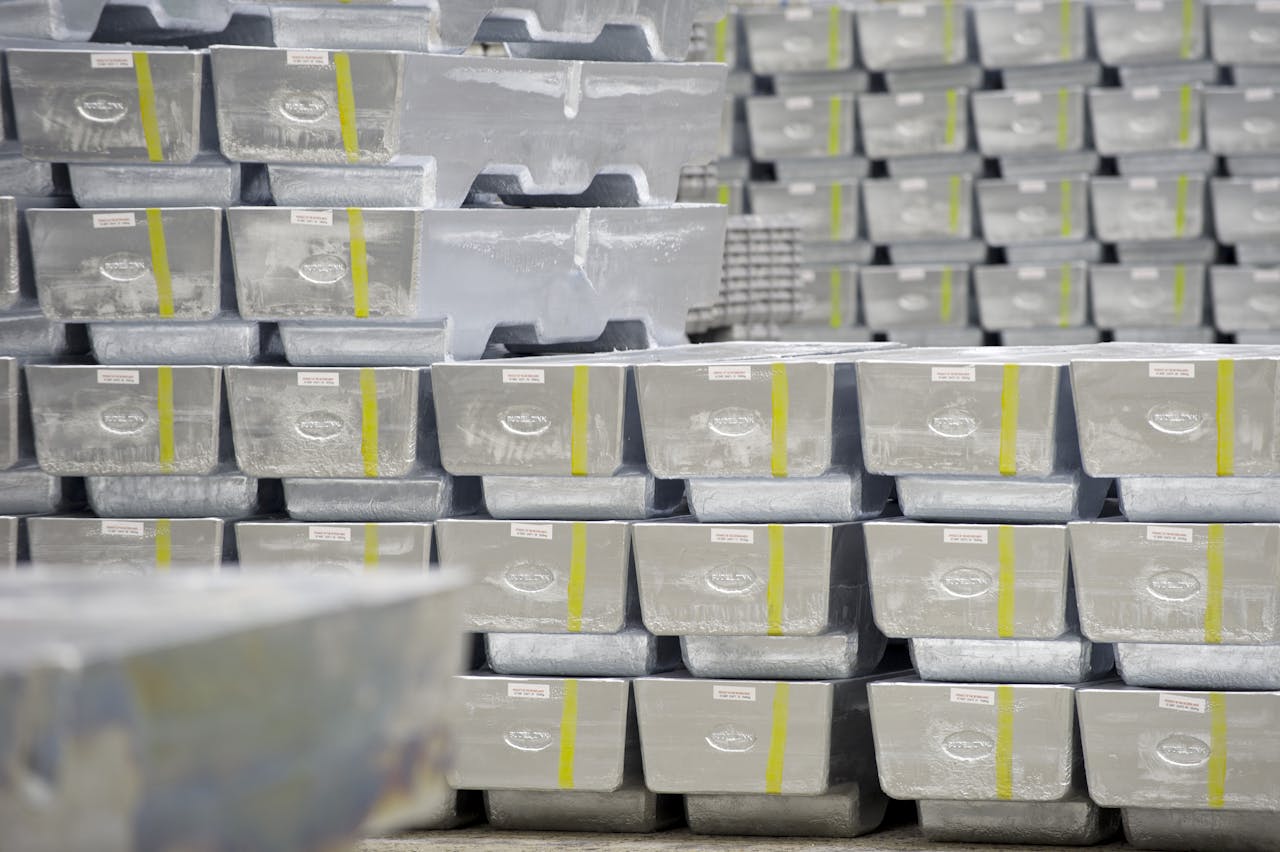
Duurzaam?
We praten nog even na met Cris Copini over het streven naar duurzaamheid, wat bij Nyrstar naar eigen zeggen hoog in het vaandel staat. Waar liggen nog mogelijkheden voor verbetering? “Het energieverbruik. Dat is hier heel hoog en dit komt vooral door de elektrolyse. We hebben hier een stroomvoorziening met een vermogen van 150 megawatt, dat is evenveel als die van de stad Eindhoven. Tegelijkertijd levert ons product weer een grote energiebesparing elders in de keten. Vroeger roestte een auto letterlijk weg, maar dat gebeurt niet meer door de beschermende zinklaag.”
De grootste bijdrage ligt waarschijnlijk in de bouw, stelt Copini. “Een verzinkte stalen constructie gaat maar liefst twaalf keer langer mee dan een onbeschermde. Dat is waarom wij zink een heel duurzaam materiaal vinden. En natuurlijk denken we goed na over ons energieverbruik en proberen we dat waar mogelijk te beperken. Ons energieverbruik in het celhuis wordt geregeerd door natuurkundige wetten, daar kunnen we niet zoveel aan doen. Maar voor de rest van het proces streven we ernaar om zo efficiënt mogelijk zink te maken.”