Uit biomassa kunnen we al kleine moleculen maken als basis voor plastics. Aromaten, die we voor onder andere PET gebruiken, zijn echter moeilijker. Het Groningse bedrijf BioBTX vond mogelijk een efficiënte oplossing voor dit probleem. Zij ontwikkelen op basis van een oud proces nieuwe technologie.
Biomassa is volgens veel wetenschappers een belangrijke duurzame bron voor materialen. Met het koolstof in plantenresten kunnen grote bedrijven al stoffen zoals ethyleen maken, een klein molecuul dat we gebruiken als de basis van het plastic polyetheen. Grote moleculen zoals benzeen, tolueen en xyleen (BTX), stoffen die we aromaten noemen en allemaal een ring van zes koolstofatomen als basis hebben, vormden tot voor kort nog een uitdaging. Maar Groningse onderzoekers van het bedrijf BioBTX hebben nu een proces ontworpen waarmee ze juist deze moleculen vrij makkelijk kunnen maken.
Niet alleen praten
Het idee ontstond oorspronkelijk bij een adviesbureau, wat uiteindelijk leidde tot de oprichting van BioBTX. BioBTX Chief Technology Officer Niels Schenk legt uit: “We wilden niet alleen maar praten, maar ook het goede voorbeeld geven. We werkten veel aan biomassa-vraagstukken en besloten te onderzoeken welke gaten in de markt we eventueel konden opvullen.” Zo ontdekten ze dat slechts twee kleine bedrijven zich bezig hielden met het maken van BTX uit biomassa. “En dat terwijl BTX toch veertig procent is van alle olieproducten die we in Rotterdam maken. Het is onder andere de grondstof voor PET, het plastic dat we gebruiken voor veel drinkflessen.”
De markt leek open te liggen, maar dan moesten ze wel een goede techniek vinden. Ze kwamen uiteindelijk uit bij katalytische pyrolyse, een technologie die onderzoekers twintig jaar geleden al onderzochten met als doel brandstoffen te maken. “Daar deden ze precies wat wij wilden doen: biomassa omzetten in BTX”, vertelt Schenk. “Dat proces was alleen nog niet schaalbaar en efficiënt genoeg, dus hebben wij het in samenwerking met de Rijksuniversiteit Groningen en het chemische bedrijf Syncom verder getest en geoptimaliseerd.”
Drie stappen
Het proces bestaat uit slechts drie stappen. De eerste is zogenaamd thermisch kraken, ook wel pyrolyse genoemd. In dit proces verhit je de biomassa zonder dat je er zuurstof bij laat komen. “De netwerken van koolstof in de biomassa vallen onder die omstandigheden uit elkaar tot kleine stukjes van zo’n twee of drie koolstofatomen lang”, legt Schenk uit. Deze kleine stukjes leid je vervolgens langs een katalysator die ervoor zorgt dat ze op een selectieve manier weer aan elkaar binden. Schenk: “We hebben de katalysator zo ontworpen dat er een mengsel van benzeen, tolueen en xyleen ontstaat.”
Vanwege de hoge temperaturen zijn alle producten op dat moment nog gasvormig, dus in de laatste stap koel je de boel af zodat je een vloeibaar product overhoudt. Dit is dan nog steeds een mengsel, maar dat is volgens Schenk geen probleem omdat veel fabrieken het mengsel gebruiken. “Maar je kunt het ook scheiden als je een van de componenten puur wilt verkopen. Dat is allemaal bekende technologie.”
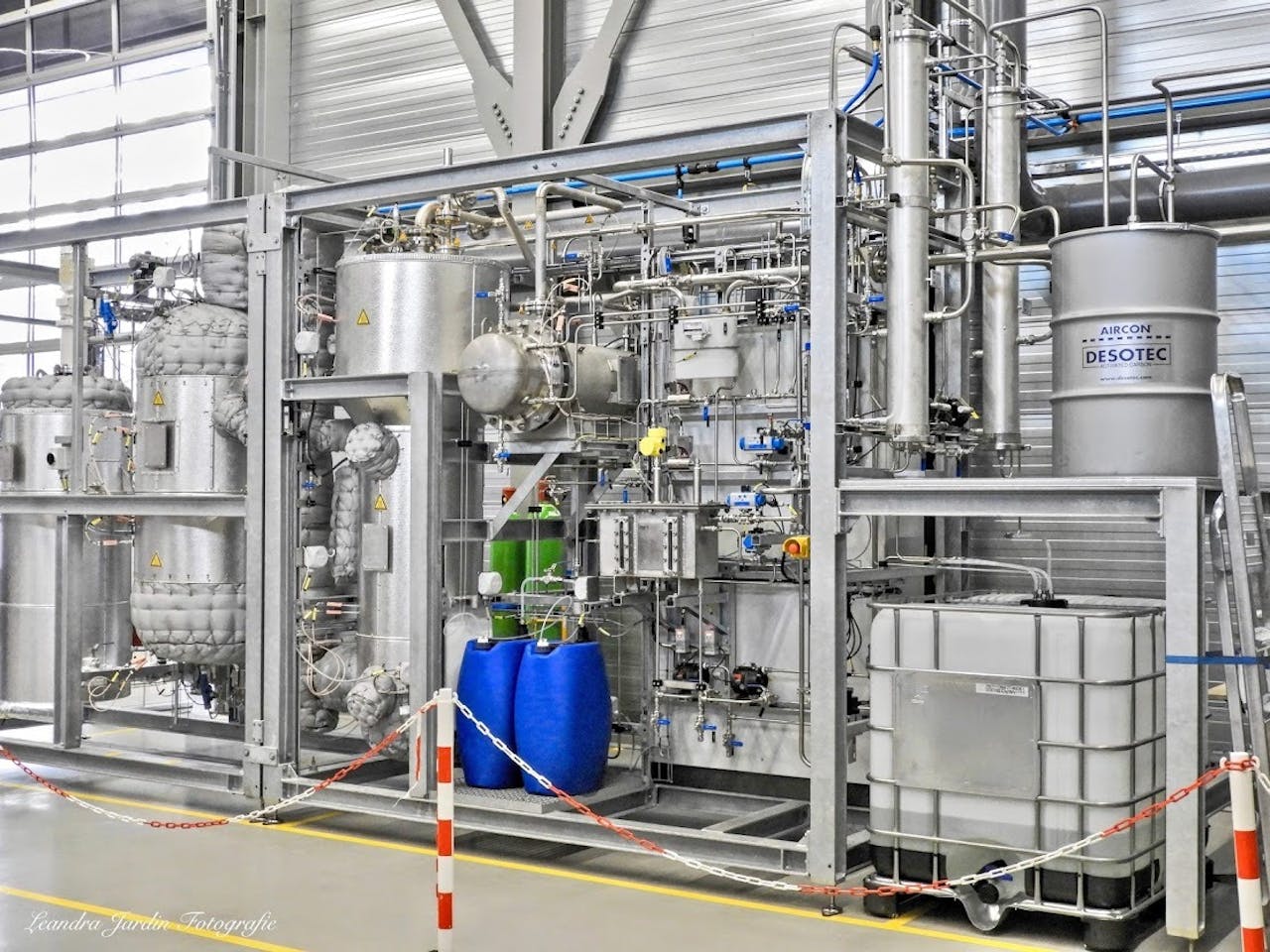
De pilot plant van BioBTX, waar ze biomassa omzetten in benzeen, tolueen en xyleen.
Leandra Jardin Fotografie, via BioBTX met toestemmingCirculair
Inmiddels heeft het bedrijf een zogenaamde pilotplant gebouwd waarin ze de reactie testen. Deze opstelling draait op ruwe glycerine, een soort biomassa, maar volgens Schenk is het proces erg flexibel. “In theorie kunnen we eigenlijk alle biomassa gebruiken die we kunnen vinden. Het maakt ook niet uit als er verschillende soorten door elkaar zitten, want we breken alles even goed af.” Het mengsel moet alleen niet te nat zijn. “Dan gaat er te veel energie in het verdampen van water, dat is zonde.”
BioBTX wil in ieder geval zo circulair mogelijk werken. De glycerine bijvoorbeeld is een afvalproduct van SunOil uit Emmen, dat biodiesel maakt uit frituurolie. Ook kijken ze nog naar andere koolstofbronnen. “In het lab testen we ons proces nu op gemengd plasticafval”, vertelt Schenk. “Dit werkt al redelijk goed, dus we kijken naar de mogelijkheden om deze optie ook in te bouwen in onze pilotplant.”
Voorbeelden
Met het product uit de pilotplant maakte BioBTX in samenwerking met andere bedrijven al een paar plastics, om te laten zien dat het gelijk is aan fossiele BTX. “We werken nu bijvoorbeeld samen met chemiebedrijf Teijin, die maken Twaron-vezels voor bijvoorbeeld kogelvrije vesten. Die vezels gaan ze nu maken met onze biobased BTX.” Maar al deze toepassingen betekenen niet dat het proces al perfect is. “We proberen het proces natuurlijk nog steeds te verbeteren door bijvoorbeeld de katalysator te optimaliseren. En op termijn willen we ook de warmte die we gebruiken zelf opwekken.”